






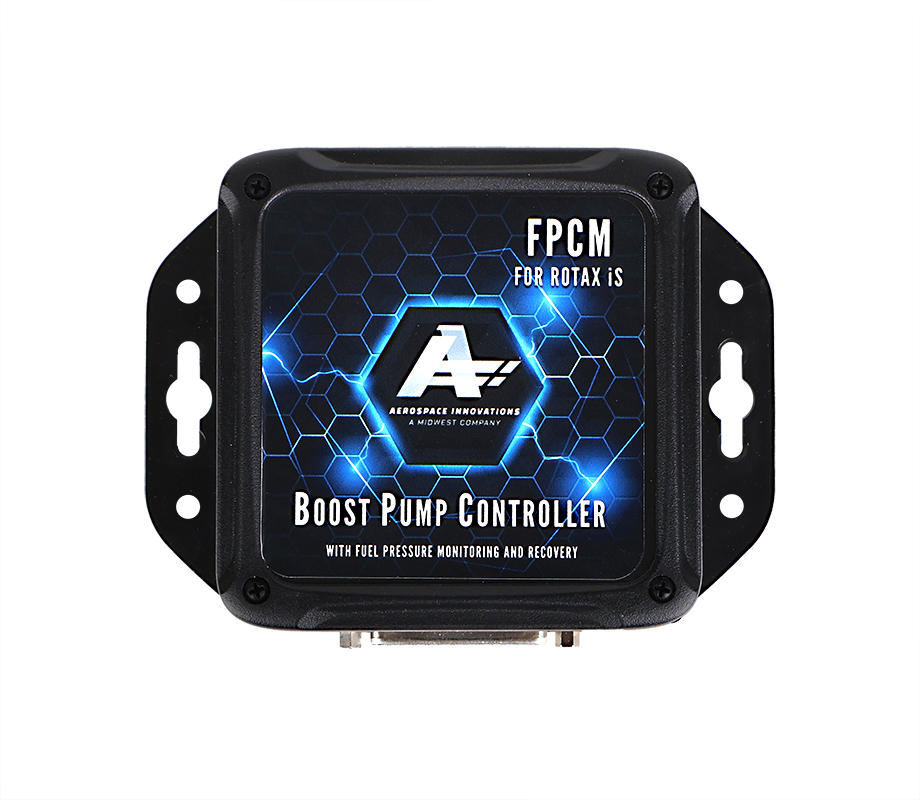
What is Included?
Base System
The base system consists of the Fuel Pump Control Module (FPCM), fuel selector valve smart sensor with mount ring and installation hardware, two boost pumps and two filters, connectors, and switches.
TSi Wing Mounting Kit
Get everything you need to mount the boost pumps in the wing without the need to drill holes. This kit includes the mounts for right and left with support for lang range tank pumps, all the plumbing to lead from the tank and connect to the aircraft fuel system as well as any needed hardware.
Available Add-ons
Transfer Pump
The transfer pump add-on includes two pumps, mounting plates to attach to the main mounts with hardware, and plumbing needed to connect to main fuel system.
Harness
For those who are looking to retrofit the system or are not using our services for their harness can purchase a system harness.
don't let low pressure get you
Vapor Lock, What’s the problem?
Reid vapor pressure (RVP) is a common measure of the volatility of gasoline and other petroleum products. It is defined as the absolute vapor pressure exerted by the vapor of the liquid and any dissolved gases/moisture at 37.8°C (100°F)
When the pressure exerted on a liquid is equal to or lower than it’s vapor pressure that liquid will start to boil. The pressure at which that liquid will boil is directly linked to the temperature of the liquid. At one atmosphere or 14.7 psi water will boil at 100°C (212°F), but if we expose the water to a pressure of only .5 psi we can boil water at room temperature. This is the reason the boiling point of water lowers with altitude, in fact at 10,000ft, water will boil at approximately 194°F
While learning about Pitot Static systems during primary training we would have all learned that we lose approximately 1 inHg per thousand feet of altitude gain, this is how an altimeter can show us altitude gains or losses and how a vertical speed indicator can tell us how fast we are climbing or descending. 1 inHg is equal to .491 psi, to determine the approximate pressure at any given altitude we can simply obtain an altimeter reading and do some math. Since this reading is the pressure at sea level for any given location, take the current reading and subtract 1 inHg for every thousand feet and multiply it by .491 to find the pressure at your altitude.
Armed with this knowledge we can now dig into the issue at hand and we will look no further than the automotive world. Our cars and trucks would also suffer from vapor lock if not for one simple solution, in fact carbeurated vehicles of the past did have this very issue, however the invention of fuel injection put this problem in the rear view mirror. Prior to fuel injection most fuel pumps were either on the engine or mounted on the chassis somewhere. with fuel injection came the need for higher pressure fuel to allow a good stream of fuel to pass through the very fast opening of the fuel injectors needle, and the electric pump as we know it was born, since electric pumps are much more efficient at pushing then pulling and to keep the pump cool, it was to be located in the tank. This location allowed the pumps to put a high pressure (approx 45psi) on the feed line all the way from the tank to the engine and in turn eliminated the previous issues of vapor lock.
A typical Rotax setup.
The Rotax iS series engines have fuel pumps that are controlled with switch inputs to the Engine Control Module and powered off the Rotax fusebox by way of the supplied wire harness. Due to this, the fuel pumps are often located in a position to allow the connectors on the harness to reach the fuel pumps, this usually means up on or near the firewall which also means there will be not only a good amount of distance between the tank and the pumps but the pumps will likely be higher than the tanks on a low wing aircraft.
While the Rotax pumps have no issue pressurizing the lines to the engine, they actually have an adverse effect on the feed line from the tank. Testing has found that with both pumps on the pressure drops by as much as 2-3 psi below ambient pressure and with one you will drop by 1-2 psi, this is a big negative effect when looking at the total pressure exerted on the feed side fuel. During testing we found that once vapors are introduced to the Rotax fuel pumps, cavitation occurs and the system fuel pressure drops well below the pressure needed to keep the engine running, switching on the second pump does indeed increase flow from the tank allowing partial recovery of the fuel pressure, we have also found that the even with 2 pumps on the cavitation can occur again once the flow is settled. Though 2 pumps should be used during takeoff and landing as well as initial climb, evidence shows that with the Intelligent Fuel Boost System you should only run on one during cruise
The RVP of fuel will differ in Summer vs Winter and even State to State. Higher elevation locations such as Utah have lower RVP limits then the lower elevation states and winter states can have an RVP as high as 15 psi while the nation wide maximum during the summer months are 9 psi. AvGas is even a bit lower at about 7 psi due to the fact aircraft fly at higher altitudes. If we remember that these numbers are based on 100°F then we could say that if we had winter fuel in our tanks and that fuel was 100°F we would not be able to start the engine at sea level without trouble. Though the chances of having a winter blend in this situation is not very likely, if you are one who lives in a cold weather state with winter fuel and you do not fly until one very hot summer day, you may want to drain your tanks.
Now we will look at a very possible scenario. Let’s say you are in Arizona on a 100°F day and your RVP 9 MoGas is heat soaked from sitting in your tanks. The altimeter is 29.92 inHg (14.7 psi) at sea level but the elevation of your airport is 2,000ft msl. You start up and take off with 2 Rotax pumps, starting with a sea level pressure of 14.7 psi, we will subtract 2 inHg (.98 2psi) for the field elevation as well as the 2 psi loss from both Rotax pumps and we get an absolute pressure in the feed line of approximately 11.7 psi, so far so good. Now you start a climb to 10,000ft to get over the mountains, the fuel in your tanks will take a while to cool since liquid takes some time to change temperature. Climbing through 8,000ft the pressure in the feed line will now change by about 3psi (6,000ft above field elevation times .491 psi per thousand feet), this now gives a pressure of 8.7 psi right on the edge. If you turn off one Rotax pump we can bump that up to 9.7 psi but upon reaching 10,000ft you are back in the same situation. With certain conditions even Avgas can be effected and has been reported in areas of high elevation and temperature.
How Does the Intelligent Fuel Boost System Work?
Through static testing we found that by placing pumps at the wings we can boost the pressure on the feed side to not only overcome the negative effect of the Rotax pump but to increase it it enough to protect against most scenarios. This testing helped us find the right balance between having enough pressure, but not too much for the Rotax fuel system to handle.
Our flight testing has shown that not only do we overcome the 2 psi below ambient penalty of the Rotax pumps but we can add another 5-6 psi, which gives us a good amount of extra breathing room. Even with RVP 9 at 100°F you could climb to 18,000ft on a standard day and still be comfortably on the plus side.
One draw back to having pumps at the wings is that they are located before the fuel selector valve, only one wing will have a path to the engine at a time leaving one to dead head against the fuel selector. To remedy this we will need to have a switch that can be toggled whith each switch tanks, though possible, this would be more to maintain and would honestly be a hassle. We developed an automatic sensing system that fits onto your current Andair fuel selector with some modifications to the fuel valve mounting shroud. With this in place, only the pump of the selected tank will operate removing the need to manually manage this switching.
How about Safety?
We thought about that as well and we do have a few safety tricks up our sleeves.
First, we have built in discrete alerts to connect to either an LED or your G3X system to alert you of problems.
Second, upon power up, the system does a self test to determine if the pumps circuits are complete and the pumps are capable of working electrically. If faulty, the fail discrete will activate.
Third, we thought about what happens if the position sensing circuit or the module controlling the system were to fail? We designed the pumps to default on if the system can’t determine a fuel selector position which will activate the fail discrete will activate or if the controller failed. The pump we selected was tested to handle the dead heading in the unlikely event the system were to fail safe to on.
Fourth, we monitor the system fuel pressure to ensure that the Rotax pumps are providing proper pressure. Since it is better for feed pressure to operate on one Rotax pump during climb and cruise, we designed the system to turn on both Rotax pumps in the event the pressure drops. Since this happens faster than you may be able to detect, we also activate a discrete to warn you of the pressure drop and Rotax pump activation.
Fuel Selector Shroud
The original fuel selector shroud for the TSi has a narrower body where the selector body fits and the face where the selector plate rests is smaller in diameter, the later one was increased in size to help create space for the hoses to connect to the selector. If you have the older style shroud we have 2 options availabel. The first is to upgrade to the new larger fuel selector shroud to give more space for fuel lines. We will offer these at cost to us for your convenience. For the second option we have designed a smaller fuel selector ring to accomodate the older shroud if you choose not to upgrade to the new one. See the video directly below.
Comparison Of The TSi Selector Shrouds
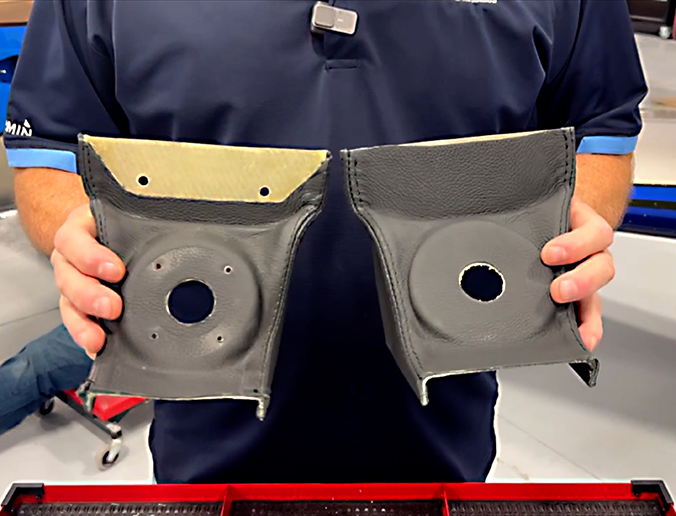
New Updated Selector Plate
For those who have the smaller TSi fuel selector shroud and do not want to upgrade to the newer shroud, or for those with a Sling 2 or any other aircraft we have developed a new Selector Ring.
Frequently Asked Questions
No, the base system is useful for and can be used on all Rotax iS equipped low wing aircraft.
Yes, the mounting kit which is currently available for the Sling TSi is not required to install the system. Once you find a suitable pump location, you can create your own plumbing.
If you wish to take advantage of the automatic Rotax pump activation you will need to connect to the fuel pressure sensor.
Yes, there is a ground discrete that can be connected to an LED lamp on the panel or to an EFIS system that will give indication of an automatic Rotax Backup Pump activation.
In the unlikely event the system fails and you need the boost pumps, the boost pump override switch will turn both pumps on manually. If the system can’t detect which position the selector is in, it will force both pumps on. If power is lost to the FPCM, both pumps will default to on so long as they are still powered.
No, the pumps used are free flow diaphragm style pumps with a spring loaded check valve. Fuel will always flow even when the pump is off.
With both pumps on all the time, the flow of pump for the tank not selected will be blocked by the fuel valve. Though this is not ideal for pump life, there will be no negative effect on the fuel system otherwise.
There are several ways to turn off the system. The first is to pull the breaker. In the event of an emergency situation, if both fuel pump switches are turned off or the fuel valve is selected to off the system will turn both of the pumps off.